What Strategies Are Effective for Maintaining Equipment Uptime in Manufacturing?
In the quest to maximize equipment uptime, we've gathered insights from CEOs and Directors who face this challenge head-on. From implementing predictive maintenance solutions to establishing routine equipment check-ups, discover the seven strategies these experts employ to keep their machinery running smoothly.
- Implement Predictive Maintenance Solutions
- Proactive Maintenance and Real-Time Monitoring
- Customize Machine Reliability Programs
- Utilize Remote Monitoring for Immediate Response
- Adopt Proactive Maintenance Strategy
- Quickly Address Digital Signage System Downtime
- Establish Routine Equipment Check-Ups
Implement Predictive Maintenance Solutions
At ADTANCE, our mission is to empower companies with innovative software solutions that not only enhance operational efficiency but also significantly improve equipment uptime. One of the primary challenges in maintaining equipment uptime is the ability to predict and prevent potential failures before they occur. To tackle this challenge, we've developed and implemented a comprehensive predictive maintenance solution that leverages the power of IoT (Internet of Things) and AI (Artificial Intelligence).
A specific example of how we've applied this solution can be seen in our work with a manufacturing client facing frequent, unpredictable downtime due to equipment failures. The unpredictability not only affected their production schedules but also had a significant impact on their operational costs.
Our approach involved the installation of IoT sensors on critical equipment to continuously monitor various parameters such as temperature, vibration, and performance metrics in real-time. This data was then fed into our AI-driven analytics platform, which analyzed the information to identify patterns or anomalies indicative of potential equipment failure.
By implementing this solution, we were able to provide the client with actionable insights and early warnings about equipment conditions that could lead to failures. This allowed for proactive maintenance activities to be scheduled during non-peak hours, significantly reducing unplanned downtime. As a result, the client experienced a notable improvement in equipment uptime, with a reduction in downtime incidents by over 30% within the first six months of implementation.
This example underscores our commitment at ADTANCE to leveraging cutting-edge technology to solve real-world challenges, ensuring our clients can achieve higher productivity, reduced operational costs, and improved equipment reliability.
Proactive Maintenance and Real-Time Monitoring
Tackling the challenge of maintaining equipment uptime involves implementing proactive maintenance strategies and leveraging technology to monitor equipment performance in real time. One specific example is the implementation of a predictive maintenance program for manufacturing machinery. By utilizing sensors and data analytics, we can monitor key indicators such as temperature, vibration, and lubricant levels to predict potential equipment failures before they occur. It allows us to schedule maintenance activities during planned downtime, minimizing unplanned interruptions to production. Regular inspections and preventive maintenance tasks, such as lubrication and calibration, help to identify and address issues early on, ensuring optimal equipment performance and maximizing uptime. A combination of predictive, preventive, and proactive maintenance approaches is essential for effectively managing equipment uptime and minimizing disruptions in operations.
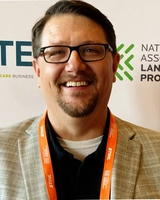
Customize Machine Reliability Programs
In my role as Executive Engineer and Sales at C-FAB LLC, I've been instrumental in designing and improving automated lubrication systems and food packaging equipment across various industries. A significant challenge we frequently encounter is maintaining equipment uptime in highly demanding production environments. From my 25 years of experience in this sector, I'm well-equipped to shed light on strategies that effectively address these challenges.
A specific example of our approach is the implementation of our Machine Reliability Programs at a large food processing plant faced with recurrent downtime due to lubrication failures. By customizing a comprehensive package of analysis, services, and equipment tailored to their specific needs, we significantly reduced their equipment downtime. We introduced automated lubrication systems that ensured precise lubrication intervals and quantities, coupled with regular analysis and monitoring to predict and prevent failures before they occurred. This not only extended the bearing and gearbox life but also increased productivity by minimizing unexpected breakdowns and maintenance costs. As a result, the plant saw a remarkable reduction in lost-time production and an increase in overall equipment effectiveness (OEE), showcasing the tangible benefits of our targeted, proactive maintenance strategies.
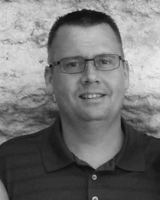
Utilize Remote Monitoring for Immediate Response
We've tackled this through the implementation of a remote-monitoring system. This innovative solution allows us to keep a constant eye on the equipment's condition from anywhere, significantly reducing downtime. A specific instance where this proved invaluable was when the system alerted us to a potential fault in one of our treadmills. Even before our users noticed an issue, we were able to remotely diagnose the problem. Thanks to this, we arranged for a technician to fix the treadmill with minimal disruption. This approach has optimized our maintenance schedule and ensured that our users enjoy a seamless fitness experience outdoors.
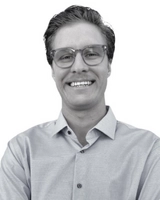
Adopt Proactive Maintenance Strategy
Maintaining equipment uptime is a critical aspect of ensuring Schmicko's operational continuity and customer satisfaction. To tackle this challenge, we have adopted a proactive maintenance strategy, which includes regular servicing and inspections, immediate addressing of any minor issues before they escalate, and maintaining a stock of essential spare parts to avoid downtime due to repairs.
For example, when we recognized that our high-pressure washers were crucial for our mobile car detailing services, we implemented a routine maintenance schedule according to the manufacturer's recommendations and trained our technicians on early fault detection.
This approach paid off notably when we encountered a potential problem with a pressure washer pump; due to our preparedness, we managed to replace the part swiftly without significant interruption to our services or inconvenience to our clients.
Quickly Address Digital Signage System Downtime
In my experience, a standout instance was when our digital-signage system faced unexpected downtime during a major event. By having a robust monitoring system in place, we quickly identified the issue—a software glitch. Within minutes, our team rolled back to a stable version, minimizing disruption. This experience reinforced the importance of not only having backup plans but also the agility to act decisively under pressure, ensuring our digital experiences remain seamless and engaging for our audience.
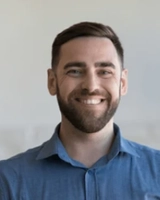
Establish Routine Equipment Check-Ups
To maintain equipment uptime, we implemented a proactive maintenance schedule, significantly reducing unexpected downtimes. For example, our printing machines are critical to our operations. We established a routine check-up and maintenance plan, performing regular diagnostics and servicing beyond the manufacturer's recommendations. This approach helped us identify potential issues before they led to breakdowns. By investing in preventative maintenance, we've ensured our equipment remains operational, supporting uninterrupted production and timely delivery to our clients. This strategy has not only optimized our operational efficiency but also reinforced our commitment to reliability and quality service in the custom apparel industry.
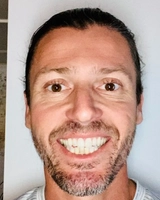