What Change to Routine Maintenance Can Positively Impact Operations?
In the quest for operational excellence, we've gathered insights from top industry professionals, including Directors and General Managers, on tweaking maintenance routines for better outcomes. From implementing structured maintenance schedules to adopting a predictive maintenance approach, explore the eight transformative strategies that have significantly improved operations.
- Implement Structured Maintenance Schedules
- Introduce Surprise Maintenance Days
- Shift to Predictive Maintenance
- Allocate Time for Innovation
- Adjust for Seasonal Maintenance
- Incorporate Regular Pressure Washing
- Adopt Preventive-Maintenance Program
- Adopt a Predictive Maintenance Approach
Implement Structured Maintenance Schedules
The implementation of a structured approach to maintenance activities has significantly enhanced operational efficiency. By introducing a carefully curated schedule, we execute tasks systematically, resulting in improved equipment reliability and reduced downtime. This change has facilitated better resource allocation and streamlined the overall workflow, ensuring that maintenance efforts align seamlessly with operational needs.
The methodical nature of the schedule enables teams to proactively anticipate and address potential issues, preventing problem escalation and minimizing disruptions to regular operations. This systematic approach not only optimizes resource utilization but also enhances the overall reliability of equipment, ultimately contributing to a more efficient and resilient operational framework. Embracing this disciplined maintenance schedule has proven instrumental in adapting to the dynamic demands of our operations, providing a solid foundation for sustained productivity and the longevity of equipment.
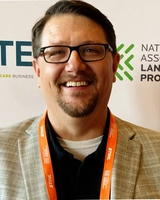
Introduce Surprise Maintenance Days
Instead of adhering strictly to a fixed routine, we designated certain days as surprise maintenance days. On these days, instead of pre-planned maintenance, we randomly selected equipment or systems for immediate attention.
This approach not only kept the team on their toes but also allowed us to catch potential issues before they escalated. The element of surprise created a proactive mindset within the maintenance team, fostering a culture of continuous improvement and efficiency. It turned routine maintenance into a dynamic and adaptive process, contributing to smoother operations and reducing unexpected downtimes.
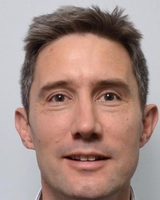
Shift to Predictive Maintenance
One impactful change to the routine maintenance schedule was implementing predictive maintenance using sensor data. By leveraging IoT devices to monitor equipment health in real-time, we shifted from traditional fixed-schedule maintenance to a more data-driven approach.
Predictive maintenance allowed us to detect potential issues before they caused downtime, optimizing equipment performance and reducing unplanned outages. This shift not only improved operational efficiency but also extended the lifespan of critical machinery, resulting in cost savings and enhanced overall reliability. The integration of predictive maintenance has proven instrumental in minimizing disruptions, contributing to a smoother and more proactive operations management strategy.
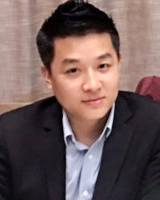
Allocate Time for Innovation
Instead of the conventional quarterly checkups, we introduced a bi-monthly 'Innovation Hour.' During this hour, our maintenance team is encouraged to step away from their usual tasks and focus solely on brainstorming creative solutions to long-standing issues. It might seem counterintuitive to allocate precious time for brainstorming in a maintenance schedule, but the results have been astonishing.
Over the months, this dedicated innovation time has yielded ingenious solutions that not only streamlined our maintenance processes but also led to cost savings and enhanced equipment reliability. This fresh perspective and regular dose of creativity have elevated our operational efficiency to new heights, making it a standout choice for enhancing operations in ways others might not have considered.
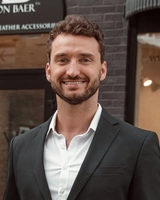
Adjust for Seasonal Maintenance
As an HVAC business owner, one impactful change we made to our routine maintenance schedule was the introduction of seasonal check-ups tailored to specific weather conditions. Historically, our maintenance was more uniform throughout the year. However, by adjusting the focus of our routine checks according to the season—prioritizing cooling system inspections before the onset of summer and heating systems before winter—we were able to provide more timely and relevant servicing.
This proactive seasonal approach not only improved the efficiency and reliability of our clients' HVAC systems during peak usage times but also enhanced customer satisfaction. Our clients appreciated the foresight in preventing breakdowns during extreme weather, and it also allowed us to manage our workload more evenly throughout the year. This strategic scheduling ensured that our team was not overwhelmed during peak seasons and could perform thorough, effective maintenance, reducing emergency call-outs and improving the overall longevity of the systems we service.
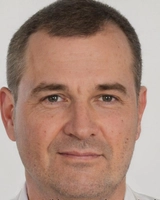
Incorporate Regular Pressure Washing
One significant change that has positively impacted our maintenance schedule is the implementation of regular pressure-washing services. As a cleaning and property services expert, I've found that many homeowners and property managers overlook the essential maintenance of exterior cleaning.
Pressure washing is not just about aesthetics; it's a preventative measure, too. Organic growth, dirt, and debris can speed up the wear and tear on your siding, driveway, and walkways. By removing these elements regularly, we extend the life of these surfaces and prevent costly replacements or damages.
Moreover, it's not just about the surfaces. When we wash gutters as part of our routine maintenance, we prevent overflow and potential water damage to the property. This might be less apparent but could lead to major issues if neglected.
Finally, regular pressure washing can contribute to health and safety. It decreases the amount of allergens, mold, and bacteria around the property, and it prevents slippery algae growth on walkways.
All in all, incorporating regular pressure washing into our maintenance schedule has improved the longevity of our clients' properties, saved them from costly repairs, and improved the overall health and safety conditions of their properties. This small routine change has had huge positive impacts.

Adopt Preventive-Maintenance Program
One significant change we made in the routine was implementing a preventive maintenance program for our sticker-production machinery. Previously, we were focused primarily on reactive maintenance—fixing things when they broke. But we realized that this approach led to downtime, disrupting our operations and deliveries.
By implementing the preventive maintenance program, we now regularly service and check the machines before any significant issues arise. This has led to a decrease in downtime and an increase in productivity.
For example, we found that by regularly lubricating and cleaning the machines, they were able to function at their optimal level, reducing wear and tear. This not only saved us on maintenance costs but also increased the lifespan of our equipment.
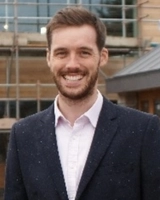
Adopt a Predictive Maintenance Approach
A notable shift from the conventional reactive method was the adoption of a predictive maintenance plan. Predictive modeling and data analysis are used in this process to identify potential problems before they arise.
We have been able to prevent problems before they occur, which has decreased downtime and increased operational effectiveness. Additionally, it has helped us prolong the life of our equipment, which has resulted in long-term cost savings.
To sum it up, implementing a predictive maintenance approach has revolutionized our operations by increasing productivity and cutting expenses. I would advise any company looking to maximize its maintenance schedule to make this adjustment.
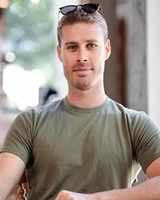