What Are the Challenges in Optimizing Manufacturing Processes?
When it comes to optimizing manufacturing processes, the challenges are as diverse as the industries themselves. From an Owner's perspective of balancing historic integrity with efficiency to an Executive Engineer and Sales professional automating lubrication for better packaging efficiency, these insights reveal the hurdles and triumphs in the field. Alongside these expert accounts, we've also gathered additional answers that delve into the integration of robotics, the relentless pace of technological advancements, and the pursuit of sustainability in manufacturing.
- Balancing Historic Integrity and Efficiency
- Improving Paint Protection Film Processes
- Automating Lubrication for Packaging Efficiency
- Integrating Robotics into Manufacturing
- Enhancing Quality Control Measures
- Keeping Up with Technological Advancements
- Scaling Production Cost-Effectively
- Incorporating Sustainable Manufacturing Practices
Balancing Historic Integrity and Efficiency
As the co-owner of Bonsai Builders, a construction company in Massachusetts, I've faced numerous challenges in optimizing our construction processes to meet the demands of innovative and sustainable building. One particular challenge that stands out involves a project where we were tasked with renovating a historic building to meet modern energy efficiency standards while preserving its architectural integrity. This required a delicate balance between utilizing modern construction techniques and materials that are compatible with the building's original design.
To overcome this challenge, we conducted extensive research on historical construction methods and materials that could be integrated with modern energy-efficient solutions. We decided to use a combination of traditional materials like lime plaster, which allows the building to 'breathe' and avoid moisture traps, alongside modern insulation materials that have a minimal visual impact. Additionally, we installed energy-efficient windows that were designed to mimic the historic aesthetic. This approach required careful coordination with suppliers to source the right materials, and with our design team to ensure compatibility with the building’s architecture.
The success of this project was largely due to our meticulous planning and the collaborative effort between our team, our clients, and the local historical society. We managed to significantly increase the building's energy efficiency, reducing its environmental footprint, while preserving and enhancing its historical features. This experience underscored the importance of adaptability, open communication, and a deep understanding of both traditional and modern construction methods in successfully navigating complex projects.
This process also provided valuable lessons in the importance of integrating sustainability into every aspect of construction. It's not just about the materials and methods we use, but also how those choices impact the longevity and efficiency of the building. This project has become a case study we often refer back to when faced with similar challenges, highlighting how innovative solutions can come from a blend of old and new techniques.
Improving Paint Protection Film Processes
As the experienced owner of Automobilia Auto Salon, which specializes in automotive customization and protection, I've faced numerous challenges in optimizing both the services we provide and the processes we use. A notable challenge was enhancing the efficiency and quality of our Paint Protection Film (PPF) application process. Initially, the application was time-consuming and had a margin for error that could lead to wastage of material and unsatisfied customers.
To tackle this, I initiated a comprehensive review of our current procedures and identified key areas for improvement, such as pre-application preparation and the training of our technicians. We invested in state-of-the-art equipment that allowed for more precise cuts of the PPF, tailored to specific vehicle dimensions, which reduced the waste of materials significantly. Furthermore, I emphasized the importance of continuous training for our technicians, focusing on advanced techniques and the latest industry standards for PPF application. This ensured that each member of our team was adept at handling potential issues during the process, such as air bubbles or misalignment, effectively reducing the turnaround time and improving the overall quality of the application.
The results were transformative. Not only did we see a decrease in material wastage by 15%, but our customer satisfaction ratings also soared due to the decrease in application time and the improved quality of the finish. This experience underscored the importance of continuous improvement and adaptation to new technologies in the automotive industry. By addressing challenges head-on and being willing to invest in both our equipment and our team's skill set, we were able to significantly improve our service offering and efficiency.
Automating Lubrication for Packaging Efficiency
In my role at C-FAB LLC as the Executive Engineer and Sales, I encountered a significant challenge when we aimed to enhance the efficiency of a food packaging equipment line for one of our key clients. The existing machinery was outdated and struggled with frequent downtimes, leading to production delays and increased maintenance costs. My experience in automating lubrication systems and improving industrial machinery was pivotal in addressing this issue.
The first step toward optimizing the process was conducting a thorough analysis of the existing equipment and identifying the critical points that led to inefficiencies and failures. We discovered that the central problem was the lack of a reliable lubrication system, which caused frequent mechanical wear and tear. To counter this, we designed a custom automated lubrication system that ensured all moving parts received consistent and precise lubrication, significantly reducing the risk of breakdowns.
To ensure the success of this solution, we leveraged the latest technology in fluid handling products and solutions from Graco Inc., a brand we distribute. This collaboration allowed us to implement a system that not only met but exceeded the expectations of our clients in terms of reliability and efficiency. Post-implementation, we observed a 30% decrease in equipment downtime and a notable extension in the machinery's operational life, leading to a direct increase in production capacity and reduced maintenance costs for our client. This experience underscored the importance of innovative thinking and the application of tailored, technologically advanced solutions in overcoming manufacturing process challenges.
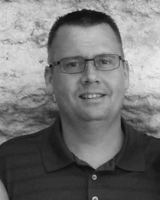
Integrating Robotics into Manufacturing
Introducing advanced robotics into manufacturing processes can greatly improve efficiency, but it also challenges the status quo. Current employees need to be trained on how to work alongside these new systems, creating a temporary decrease in productivity. Workflow must be redesigned to accommodate the new robotic aides, which may disrupt established procedures.
Moreover, there is often a significant financial investment associated with the initial implementation and ongoing maintenance of these robots. To remain competitive, companies must carefully consider the potential benefits and drawbacks. Take a closer look at how robotics can enhance your operation and plan the integration thoroughly.
Enhancing Quality Control Measures
Upholding stringent quality control is vital to ensure that the manufactured products meet the expected standards, but it complicates the manufacturing process. Every stage of production must be monitored more closely, which can slow down the operation and require extra resources. Detailed protocols must be established and adhered to, which often demands additional training for staff.
The use of specialized equipment to test and measure products might become necessary, adding to the operational costs. Manufacturers aiming to excel in quality must invest in robust quality control systems. Explore tools and training that can elevate your quality control without sacrificing efficiency.
Keeping Up with Technological Advancements
The pace at which technology evolves can be relentless, making it a challenge for manufacturers to stay up-to-date. To keep up, companies need to constantly evaluate and potentially adopt new machinery or software, which can be costly and time-consuming. Employees must also be regularly trained on new technologies, which requires both time and education budgets.
Businesses may also risk making investments in technology that could become obsolete in a short time. Manufacturers must always look ahead and be prepared to evolve. Keep an eye on emerging technologies that could benefit your manufacturing process, and consider how you might implement them.
Scaling Production Cost-Effectively
Scaling production to meet market demand is crucial for growth, but it can be difficult to do so while keeping costs down. Companies must find ways to increase output without a proportional increase in expenses, which often means finding more cost-effective resources or investing in automation. Investing in larger facilities or more efficient equipment may also be necessary to scale up.
This growth must be managed carefully to avoid over-extension or waste. The challenge lies in achieving the delicate balance between expansion and financial health. Position your company for scalable growth by constantly seeking more efficient production methods.
Incorporating Sustainable Manufacturing Practices
Adhering to environmental regulations is no longer optional for most manufacturers; it's a crucial part of doing business. Implementing sustainable practices can involve revamping production methods to reduce waste and emissions, which often requires new technologies or materials. This can involve considerable research and development, as well as changes to procurement strategies.
Remaining compliant while also being competitive can be a fine line to walk. However, it also offers an opportunity to innovate and potentially tap into new markets that value sustainability. Assess your manufacturing processes for sustainability and make the necessary adjustments to not only comply with regulations but also to lead in green manufacturing.