How Does Automation Change Workflow in Manufacturing?
In the rapidly evolving landscape of manufacturing, we've gathered insights from Presidents and CEOs to understand the impact of automation on their workflows. From increased precision and efficiency to enhanced efficiency in fabric-cutting, explore the transformative effects through these four first-hand experiences.
- Increased Precision and Efficiency
- IoT Revolutionizes Quality Control
- Streamlined Workflow with Automation
- Enhanced Efficiency in Fabric-Cutting
Increased Precision and Efficiency
Introducing automation into our manufacturing environment at CH Ellis not only increased our efficiency but also allowed for greater precision in our products. The changes were predominantly seen in our CAD-CAM manufacturing capabilities, foam-cutting processes, and cloth-cutting operations. One of the major changes we noticed soon after introducing automation was the decrease in human error and increase in accuracy in the production process.
For example, we introduced a Gerber machine for cutting cloth and foam, which greatly reduced cutting defects and dramatically increased our speed of production. It's more precise and certainly much quicker than a human could ever be, and this reduction in errors and boost in production speed directly translates into cost savings and quicker deliveries for our customers. Further, we also benefited from our waterjet and CNC router. These machines amplify the precision of our custom foam inserts, ensuring the exact fit for every product or tool into our cases.
The standardization and consistency brought by these automations ensured that each case was of the best quality, regardless of the size of the order. However, introducing automation didn’t mean we fully did away with the human touch. Many of our products, like our tool pallets, are still hand-sewn to ensure they last a lifetime. This blend of automation and craftsmanship has been the key to growing our nearly 125-year-old company into a modern cornerstone of the custom case industry.
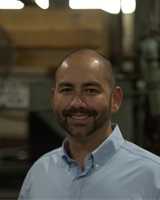
IoT Revolutionizes Quality Control
Introducing automation into our manufacturing, particularly through IoT (Internet of Things) integration, revolutionized our workflow. It's like infusing the factory with a sixth sense. A vivid example springs to mind: our inspection process. Previously, a team manually examined the sportswear, a time-intensive task prone to human error. But with IoT, sensors now meticulously scan each item for quality control, flagging even the minutest flaws. This shift accelerated the inspection phase and elevated our product quality. It's personal for me because seeing this transformation was like watching a well-orchestrated symphony—each automated part playing its role with precision, transforming our work from routine to extraordinary.
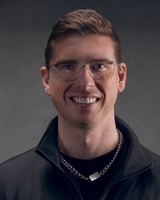
Streamlined Workflow with Automation
In our sticker printing company, I can say that introducing automation has significantly streamlined our workflow. Before automation, we had to manually operate each machine, which was tedious and time-consuming. With automation, machines are pre-programmed for tasks, saving us considerable time and effort.
A prime example of this change was in the cutting process. Pre-automation, we cut each sheet of stickers by hand, which could take upwards of five minutes per sheet. Post-automation, a machine cuts an entire sheet in mere seconds with precision. The speed and accuracy have improved exponentially, boosting our productivity and efficiency.
Moreover, automation has also helped us reduce errors and waste. The machines perform tasks consistently and with minimal human intervention, reducing the chance of human error. This has not only improved the quality of our products but also saved us a significant amount of material that would have otherwise gone to waste due to errors.
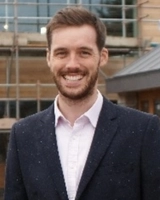
Enhanced Efficiency in Fabric-Cutting
Introducing automation into DasFlow's manufacturing environment revolutionized our workflow, significantly enhancing efficiency and consistency. One clear example is our transition to automated fabric-cutting systems. Previously, manual cutting was not only time-consuming but also prone to errors, affecting both the pace and quality of production. With automation, we achieved precision in cuts, uniformity in sizes, and a remarkable reduction in fabric waste. This change streamlined our production process, allowing us to handle larger orders more efficiently while maintaining the high-quality standards DasFlow is known for. It also freed up our skilled workers to focus on more intricate aspects of garment making, where human craftsmanship truly shines.
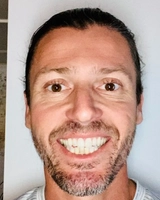