How Do You Engage a Manufacturing Team in Continuous Improvement?
In the quest to foster a culture of continuous improvement within teams, we've gathered insights starting with an Owner who implemented a suggestion system. Alongside industry professionals, we've also compiled additional answers that offer a spectrum of strategies to engage team members. From launching an innovation week to investing in team versatility, discover a variety of methods that encourage collective progress.
- Implement a Suggestion System
- Launch an Innovation Week
- Gamify Continuous Improvement
- Introduce Productivity Dashboards
- Hold Collaborative Workshops
- Reward Incremental Improvement Goals
- Invest in Team Versatility
Implement a Suggestion System
In my experience leading Automobilia, a company dedicated to automotive protection and customization, I've found that engaging our team in continuous improvement initiatives not only boosts morale but also significantly enhances our service offerings. For example, we introduced a suggestion system where any team member could propose new ideas or improvements to our protocols, especially regarding our bespoke car detailing and customization services. This open forum led to the implementation of a new workflow for our Paint Protection Film (PPF) application process, enhancing efficiency by reducing application times by approximately 20% without compromising on our renowned quality.
Additionally, tapping into our team's collective expertise allowed us to develop a more client-centric approach to custom wheels and tires selection. Staff members suggested and initiated a personalized consultation process, incorporating a deeper analysis of the client's preferences and vehicle performance needs. This adjustment not only improved customer satisfaction but also increased our revenue from customized solutions by 15% in the following quarter. These examples underscore the importance of team involvement in driving continuous improvement, showcasing a direct link between employee engagement and business success.
Launch an Innovation Week
In my tenure at C-FAB LLC, involving the team in continuous improvement initiatives has been crucial. One significant example I can draw upon involves our approach to enhancing our food packaging equipment. We kick-started an 'Innovation Week,' where team members from different departments were encouraged to present their ideas on how to improve our existing machinery designs and processes. This initiative was not only about new ideas but also addressing existing challenges with fresh perspectives.
One transformative outcome from this was the development of a more efficient, automated lubrication system for our packaging machines, significantly reducing the downtime caused by manual maintenance and increasing overall production efficiency. We saw a noticeable improvement in not just the machinery's performance but also in team morale, as they witnessed their direct contributions leading to tangible advancements. This experience underscores the value of collaborative effort and reinforces my belief that diverse inputs can drive significant innovations in even the most technical aspects of our operations.
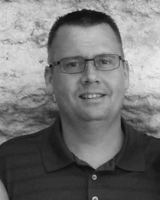
Gamify Continuous Improvement
Incorporating fun into the concept of continuous improvement can yield surprising results. By setting up gamified challenges that track and reward progress, teams become more invested in the outcome. The competitive nature of games can stimulate creativity and drive, incentivizing teams to find innovative solutions to improve efficiency.
Gamification strategies can break the monotony of regular tasks, therefore, increasing engagement and sparking a collaborative spirit among team members. To make the most of this approach, consider creating a challenge that is fair and exciting for all team members to participate in.
Introduce Productivity Dashboards
Visibility is key to fostering a culture of continuous improvement within a manufacturing environment. Introducing dashboards that show real-time data on productivity allows team members to see the immediate impact of their efforts. This transparency can help to identify areas for improvement and facilitate a sense of ownership as employees watch their contributions make a difference.
Being able to measure successes and challenges in real-time encourages a proactive mindset towards making incremental improvements. Embrace this technology to keep your team informed and motivated.
Hold Collaborative Workshops
Creating a forum for regular exchange of ideas can significantly enhance a team's capacity to improve continuously. By holding workshops focused on collaborative problem-solving, teams develop a shared understanding of challenges and learn to communicate more effectively. These sessions not only provide skills to tackle current problems but also prepare the team to anticipate and address future issues.
Such an environment nurtures a supportive community, where each member is valued for their input. Encourage your team to actively participate in the next problem-solving workshop and share their insights.
Reward Incremental Improvement Goals
Encouragement through recognition is a powerful motivator. Offering tangible rewards when the team meets incremental improvement goals helps keep members focused and eager to contribute. It establishes a clear link between effort and outcome, affirming that the hard work does not go unnoticed.
This practice also instills a habit of aiming for consistent progress rather than just final results. Reward the commitment of your team, and be sure to celebrate every milestone achieved in the pursuit of excellence.
Invest in Team Versatility
Enhancing the team's skill set is beneficial for both individual growth and the company's ability to adapt to changing demands. Through the rotation of positions, employees gain a broader understanding of the manufacturing process, which enables them to identify areas of improvement from different vantage points. This cross-training makes the team more versatile and fosters adaptability.
As employees become more knowledgeable, they tend to contribute more effectively to the team's goals. Start planning a rotation schedule to invest in the versatility of your team.