Balancing Automation With Human Expertise in Manufacturing: 7 Insights
In an era where manufacturing is ever-evolving, the balance between automation and human expertise is crucial. Founder & CEO and Managing Director share their invaluable perspectives on this dynamic. Discover how integrating AI and human insight can revolutionize operations, and why leveraging the strengths of both automation and humans is essential. This article brings together seven key insights from industry leaders.
- Integrate AI and Human Insight
- Human Insight Enhances Automation
- Combine AI and Employee Training
- AI Frees Humans for Strategic Tasks
- Human Expertise Optimizes Automation
- Technology Requires Human Expertise
- Leverage Strengths of Automation and Humans
Integrate AI and Human Insight
Balancing automation and human expertise is essential in manufacturing. My journey from medicine to business sharpened my understanding of diagnosing inefficiencies, whether in healthcare or manufacturing. At Profit Leap, we employed AI and robotics for automation but always ensured that human insight was valued, much like a diagnostic process in medicine where a machine aids but does not replace the doctor.
A specific case was when we helped a manufacturing client increase efficiency by 30% through AI-driven processes, yet the real success was integrating human expertise by training employees to oversee and optimize these automated systems. This synergy ensures that machines handle repetitive tasks while humans focus on process improvement and innovation, boosting overall productivity.
In terms of strategy, I always emphasize the 8 Gears of Success framework that combines tech and human elements for business growth. For example, after automating billing and invoicing with Robotic Process Automation, a 90% error reduction was achieved, freeing the team to improve strategic tasks—an approach applicable across industries to improve efficiency without losing the unique value of human expertise. In my journey from medicine to business strategy, I've learned that the key to balancing automation and human expertise lies in leveraging each for what they do best. Automation excels in handling repetitive and data-intensive tasks. For instance, in one of my ventures, we used AI for process automation, which reduced errors in invoicing by 90%. This freed up our team to focus on strategic decision-making and innovation rather than mundane tasks.
Human expertise, however, remains crucial for interpreting data and making nuanced decisions. In my experience expanding a diagnostic imaging company, it was the trained professionals who could analyze complex imaging results, a task automation couldn't replicate. They provided the critical interpretive insights that ensured accurate diagnoses and improved patient care.
Combining these strengths allows businesses to achieve operational excellence. Think of automation as the enabler of efficiency and human expertise as the driver of strategic growth. Training staff to complement automated systems rather than replace them ensures that we're using the full potential of both worlds, enhancing both productivity and innovation across the board.
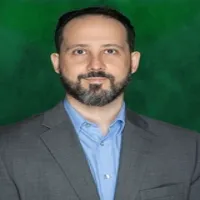
Human Insight Enhances Automation
Balancing automation with human expertise in manufacturing is a strategic art I've honed over 40 years at Altraco. Automation improves efficiency, but it's the human expertise in navigating the nuances of global supply chains that sets the best apart. In our experience, human insight is crucial for understanding complex systems and subtle variations in product design that machines might miss. For instance, when we faced quality issues in overseas manufacturing, implementing a multi-point inspection process led by skilled inspectors was key. This proactive human intervention caught potential defects early, ensuring product excellence without major delays.
One vivid example is our collaboration with a leading sporting goods company. We employed automation for repetitive tasks to streamline production yet relied heavily on skilled professionals to manage cultural gaps and ensure communication clarity with our overseas partners. Their expertise in managing relationships and expectations resulted in a 15% reduction in production errors, underlining how human skills complement technological advancements. This synergy enables businesses to not only maintain high standards but to adapt to and thrive in evolving market landscapes.
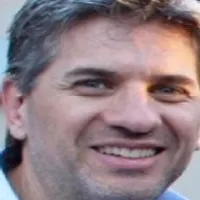
Combine AI and Employee Training
Navigating the intersection of automation and human expertise in manufacturing is crucial for efficiency and innovation. In my role as co-founder and CFO of Profit Leap, I've seen how integrating AI and automation can significantly optimize operations. For example, deploying AI-driven data analysis can uncover inefficiencies in manufacturing, allowing businesses to target specific areas for improvement, like reducing cycle times without overwhelming the staff.
However, the human element is indispensable. By combining automation with comprehensive employee training, businesses improve both machine effectiveness and employee satisfaction. Skilled workers can focus on higher-level insights and problem-solving, further driving growth. This balanced use of technology and human expertise has resulted in an average revenue growth of 22% for companies I've worked with, ensuring sustainable progress.
AI Frees Humans for Strategic Tasks
Balancing automation with human expertise is crucial, especially in manufacturing. From my experience at Next Level Technologies, I've seen how AI-driven automation improves efficiency by handling routine IT maintenance and monitoring tasks. This allows human experts to focus on strategic problem-solving, which is essential in manufacturing environments where nuanced decisions are needed.
In a specific case, we worked with a manufacturing firm struggling with network reliability. By automating system diagnostics and backups, we reduced downtime by 40%, freeing their team to innovate on production processes. This blend of technology and human input not only improved operational efficiency but also improved the company's agility.
Human expertise is key in understanding and interpreting complex data from these automated systems. By empowering staff with the right tools and training, we create environments where technology aids but doesn't overshadow the critical human decision-making process. This approach ensures both peak operational efficiency and innovative growth in manufacturing.
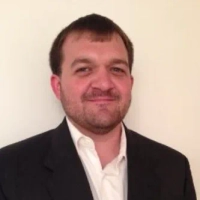
Human Expertise Optimizes Automation
With our contract-packaging factory, we have found that automation certainly helps with bringing price points down for clients (versus semi-automatic or manual processes). However, even with automation, having a human understand the equipment and its behaviors, have the ability to analyze and make adjustments, and understand how products may interact with the equipment are all key elements to success. This happens both prior to the start of a project, but also during the production process, sometimes with tiny adjustments that a machine operator can make to optimize equipment performance and product output.
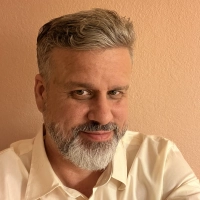
Technology Requires Human Expertise
Technology cannot replace human expertise in manufacturing. The design of technology systems to automate the manufacturing process requires expertise from the workers and supervisors of that process. Even after the system is designed and implemented, human expertise is needed to optimize the system by reviewing the data collected.
For example, using computer vision to monitor worker safety on tasks that are dangerous if not done properly can quickly build trust in technology with front-line workers, especially if that technology is connected to the machines being operated and could stop them in the event a worker is about to injure themselves. Computer vision technology can detect minuscule measurements and prevent accidents from happening if a worker gets too close to a cutting blade or grinder.
While technology may displace jobs on the manufacturing line, it does not displace the need for human expertise. Ideally, companies implementing automation and technology are upskilling their staff to manage those systems. If fewer workers are needed, ideally, there are outplacement services provided as a part of the labor optimization.
Balancing human expertise with automation and technology really comes down to how you manage your labor on the manufacturing line. As automation increases, the importance of continuous process improvement and technology aptitude also increases. The labor pool with these skills demands higher salaries and will require companies to provide different incentives to retain them. Neither of these issues should dissuade companies from making the leap into automation and technology to improve their manufacturing.
Leverage Strengths of Automation and Humans
Balancing automation with human expertise in manufacturing is about leveraging each for their strengths to drive efficiency and innovation.
Automation excels at repetitive tasks, consistency, and scalability. It reduces errors and enhances output quality, which is vital in competitive industries. Technologies like robotics, AI, and IoT streamline operations, minimize costs, and address labor shortages effectively.
However, human expertise remains irreplaceable for creative problem-solving, strategic decision-making, and adapting to unique or unforeseen challenges. Humans bring context, innovation, and emotional intelligence to the table—critical for managing exceptions and fostering customer relationships.
To balance the two:
Strategic Integration: Use automation to handle routine tasks, freeing up humans to focus on higher-value activities like innovation and strategic planning.
Collaboration Tools: Foster environments where humans and machines work cohesively. For example, data analytics platforms can guide human teams to make informed decisions.
Upskilling Workforce: Invest in training to ensure employees are proficient in using advanced tools, shifting their roles from operational to strategic.
Ultimately, balance is achieved by understanding where each element excels and designing systems that combine their strengths, ensuring sustainable growth and a competitive edge.
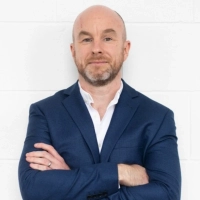