Balancing Automation and Human Creativity in Manufacturing: 6 Examples
In today's manufacturing landscape, the synergy between cutting-edge automation and invaluable human expertise is reshaping industries. From AI-enhanced quality control to collaborative robots on assembly lines, innovative technologies are amplifying human capabilities rather than replacing them. This blog explores six compelling examples of how manufacturers are striking the perfect balance between technological advancement and human ingenuity, paving the way for smarter, more efficient production processes.
- Cubic Balances Automation and Expertise in Logistics
- AI Enhances Quality Control in Manufacturing
- Cobots Revolutionize Assembly Line Collaboration
- Predictive Maintenance Boosts Equipment Efficiency
- IoT Enables Real-Time Smart Factory Decisions
- Augmented Reality Empowers Manufacturing Workers
Cubic Balances Automation and Expertise in Logistics
While we at Cubic aren't manufacturers ourselves, we work daily with manufacturers globally who use our digital freight forwarding platform. The balance between automation and human expertise is a critical equation we've helped our manufacturing clients solve in their supply chains.
Our manufacturing customers initially came to us frustrated with traditional freight forwarding that was either too manual (causing delays) or too automated (lacking expertise during disruptions). We developed a hybrid approach that's proven particularly effective for mid-sized manufacturers.
For example, one electronics manufacturer in Southeast Asia automated their shipment tracking and billing management through our platform, reducing processing time by 68%. However, when the Red Sea crisis emerged, our human operations team immediately stepped in to reroute their shipments and negotiate emergency capacity, something no algorithm could handle effectively.
What we've learned is that the sweet spot isn't complete automation or complete human handling; it's strategic automation of predictable processes while preserving human intervention for exceptions and relationship management. Our most successful manufacturing clients now use our platform to handle 80% of routine freight tasks automatically while dedicating their logistics teams to strategic supplier negotiations and contingency planning.
The key lesson: don't automate everything just because you can. Instead, map your processes and identify which ones truly benefit from human judgment versus which are ripe for digital transformation. When manufacturers approach automation this way, they typically see both higher efficiency and more engaged employees whose time is freed for creative problem-solving.
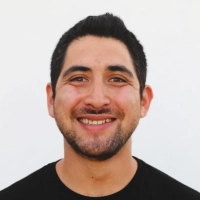
AI Enhances Quality Control in Manufacturing
AI-powered quality control systems are revolutionizing precision manufacturing processes. These advanced systems use complex algorithms to detect even the tiniest flaws in products, ensuring higher quality standards than ever before. By analyzing vast amounts of data in real-time, AI can identify patterns and predict potential issues before they occur.
This proactive approach not only improves product quality but also reduces waste and increases overall efficiency. Human creativity still plays a vital role in designing these systems and interpreting their results. Manufacturers should consider implementing AI-powered quality control to stay competitive in today's fast-paced market.
Cobots Revolutionize Assembly Line Collaboration
Collaborative robots, also known as cobots, are changing the game in assembly lines by working alongside human workers. These robots are designed to be safe and easy to program, allowing them to take on repetitive or physically demanding tasks. This frees up human workers to focus on more complex, creative aspects of the manufacturing process.
Cobots can learn new tasks quickly, making them adaptable to changing production needs. The combination of robot precision and human problem-solving skills results in improved productivity and product quality. Factory managers should explore the potential of collaborative robots to enhance their workforce's capabilities.
Predictive Maintenance Boosts Equipment Efficiency
Predictive maintenance is a game-changer for manufacturing equipment uptime and productivity. By using sensors and data analysis, machines can now alert technicians to potential problems before they cause breakdowns. This proactive approach significantly reduces unexpected downtime and extends the life of expensive machinery.
Predictive maintenance also allows for more efficient scheduling of repairs, minimizing disruptions to production schedules. The data collected can provide valuable insights into equipment performance, helping companies make informed decisions about upgrades or replacements. Plant managers should consider implementing predictive maintenance strategies to optimize their operations and reduce costs.
IoT Enables Real-Time Smart Factory Decisions
Smart factories are embracing the Internet of Things (IoT) to enable real-time decision-making. Connected devices and sensors throughout the production process generate a constant stream of data. This information is analyzed instantly, allowing managers to make quick, informed decisions about production adjustments, resource allocation, and supply chain management.
Smart factories can respond rapidly to changes in demand or supply chain disruptions, increasing overall agility and competitiveness. The integration of IoT also improves energy efficiency and reduces waste by optimizing resource use. Manufacturing leaders should investigate how IoT technologies can transform their facilities into smart factories.
Augmented Reality Empowers Manufacturing Workers
Augmented reality (AR) is proving to be a valuable tool in assisting workers with complex manufacturing tasks. By overlaying digital information onto the real world, AR can provide step-by-step instructions, highlight important components, or display real-time data directly in a worker's field of view. This technology reduces errors, speeds up training processes, and allows less experienced workers to tackle more complex tasks with confidence.
AR can also facilitate remote expert assistance, enabling skilled technicians to guide on-site workers through difficult procedures from anywhere in the world. Plant managers should explore the potential of augmented reality to enhance worker performance and streamline complex operations.