7 Ways to Achieve Seamless Data Integration Across Manufacturing Systems
Discover the essential strategies for achieving seamless data integration in the complex world of manufacturing systems, drawing from the wisdom of seasoned experts. This article demystifies the process, tackling challenges such as incompatibility between data formats, inconsistent data quality, and the need for centralized data management. With expert-backed insights, learn how to navigate the technological advancements and integration platforms that are shaping the future of manufacturing.
- Overcome Incompatibility Between Data Formats
- Address Inconsistent Data Quality
- Standardize Data Formats and Structures
- Implement Centralized Data Management
- Utilize Industrial IoT Platforms
- Adopt Microservices-Based Architecture
- Leverage Cloud-Based Integration Platforms
Overcome Incompatibility Between Data Formats
What is the biggest challenge in achieving seamless data integration across different manufacturing systems?
One of the biggest roadblocks to seamless data integration in manufacturing is the incompatibility between different data formats, structures, and communication protocols. Many legacy systems weren't designed to interact with modern IoT platforms, cloud solutions, or AI-driven analytics tools, which leads to data silos, complex transformation requirements, and delays in decision-making.
For example, older SCADA and MES systems often use proprietary protocols, while modern IIoT devices rely on standards like MQTT or OPC UA. This lack of a common data exchange standard creates major bottlenecks, requiring extensive data mapping and validation to maintain consistency across platforms. As a result, manufacturers face data quality issues, inefficient workflows, and higher integration costs when trying to unify these systems.
How did we address this challenge?
To tackle these integration issues, we implemented a middleware-based industrial data platform that streamlined data communication across all systems. Here's how we made it work:
1. Edge Computing for Data Standardization
- We deployed edge gateways to collect raw data from legacy equipment and convert it into a unified format (e.g., JSON or OPC UA) before sending it to our central data hub.
- This ensured structured, consistent data across all systems, eliminating inconsistencies from different sources.
2. API & Protocol Bridging
- By integrating middleware that supports multiple communication protocols (Modbus, OPC UA, MQTT, and REST APIs), we enabled real-time data exchange between ERP, MES, and IIoT devices.
- This drastically reduced manual intervention and eliminated data mismatches between platforms.
3. Real-Time Data Processing & Analytics
- Instead of relying on batch processing, we implemented streaming analytics to clean, transform, and analyze data in real time.
- This allowed for faster decision-making and improved overall operational efficiency.
What was the impact?
- 40% reduction in integration time, allowing faster deployment of new technologies.
- Significant improvement in data accuracy, reducing errors in analytics and reporting.
- 15% increase in production efficiency by enabling real-time monitoring and predictive maintenance.
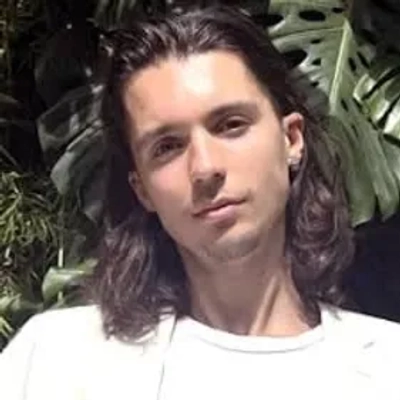
Address Inconsistent Data Quality
In my experience, the biggest challenge in achieving seamless data integration across different manufacturing systems is inconsistent data quality. Different sources often bring varying formats, missing fields, and duplicate entries, making it hard to trust the data for decision-making. For example, I've seen cases where incomplete production data led to delays in inventory planning, underscoring how critical it is to address these issues upfront.
To tackle this, we established a data cleansing and validation process for a client who was struggling with inaccurate reports. We worked on identifying errors like incorrect data types and duplicate records before integration. Standardizing formats and applying validation rules helped align the data from different systems. These steps ensured that their dashboards reflected accurate and consistent metrics, improving operational efficiency.
Another key step is creating clear data mapping and governance guidelines. This includes defining how data from each system fits into a unified schema and setting standards for quality and access control. For critical operations, real-time synchronization tools are a game-changer. They ensure that updates in one system are immediately reflected in others, preventing costly delays. Consistent data integration starts with solid groundwork, and focusing on these areas makes a noticeable difference.
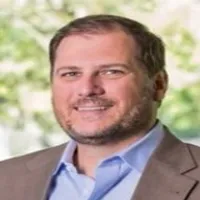
Standardize Data Formats and Structures
Standardizing data formats and structures is vital for consistent information flow between manufacturing systems. It ensures all data is compatible, making it easier to analyze and use. This uniformity reduces errors and data mismatches, which can slow down processes.
Consistency helps in setting clear expectations and outcomes for all departments involved. By doing this, facilities can enhance their efficiency. Start standardizing your data formats to streamline your operations today.
Implement Centralized Data Management
Implementing a centralized data management system allows for easy access and control of information from various sources. It acts as a single point where data is collected, stored, and managed. This method simplifies the tracking and analysis of data across different departments.
It eliminates the complexities of dealing with multiple databases. It ensures that accurate and timely information is always available. Consider setting up a centralized data management system to keep your data organized.
Utilize Industrial IoT Platforms
Utilizing Industrial IoT platforms enhances connectivity between machines and systems in a manufacturing setup. These platforms enable real-time data sharing and monitoring, which is crucial for making quick decisions. Improved connectivity helps in identifying issues and optimizing processes.
It also reduces downtime by allowing predictive maintenance. This integration leads to better productivity and operational efficiency. Explore Industrial IoT platforms to boost your manufacturing capabilities.
Adopt Microservices-Based Architecture
Adopting a microservices-based architecture breaks down complex applications into smaller, manageable services. Each service can be developed, deployed, and scaled independently. This flexibility allows for quicker updates and efficient troubleshooting.
It promotes better resource utilization and faster response times to market changes. Microservices architecture supports continuous improvement in manufacturing processes. Start incorporating microservices in your architecture for more agility.
Leverage Cloud-Based Integration Platforms
Leveraging cloud-based integration platforms provides scalable and cost-effective solutions for data integration. These platforms offer flexibility and accessibility, allowing data to be accessed from anywhere. Cloud solutions support large volumes of data and help in managing peak loads without significant investment in infrastructure.
They also facilitate seamless integration of various systems and applications. This ensures continuous data flow and business continuity. Look into cloud-based platforms for your data integration needs.