7 Steps for Handling Deviations During Batch Runs to Maintain Quality
Picture this: you're in the middle of a critical batch run when a deviation from standard operating procedures occurs. Entrepreneurs & Founders know the stakes are high, and quick decisions are essential. This article brings together seven key insights, starting with the importance of identifying and addressing deviations immediately and concluding with conducting thorough root cause analysis. Dive in to discover expert strategies for minimizing risk and maintaining quality during unexpected disruptions.
- Identify and Address Deviations Immediately
- Blend Proactive Planning and Adaptive Strategies
- Halt Operations and Analyze Causes
- Monitor in Real-Time for Irregularities
- Implement Pre-Defined Contingency Plans
- Integrate Automated Quality Checks
- Conduct Thorough Root Cause Analysis
Identify and Address Deviations Immediately
Deviations are inevitable, but how you respond defines your brand's integrity. Identify the deviation immediately-time is critical. Pause the batch if necessary. Conduct a root cause analysis with the team on the spot; transparency fosters solutions, not blame. Document every detail-this protects future runs and regulatory compliance.
Mitigate risk by having a robust quality control system: real-time monitoring, clear escalation protocols, and pre-approved corrective action plans. Train staff continuously-knowledge is the best defense against human error.
Quality isn't negotiable. If a batch falls below standard, discard it-never compromise for the sake of cost. Customers trust consistency. Protect that trust like it's your brand's most valuable asset-because it is.
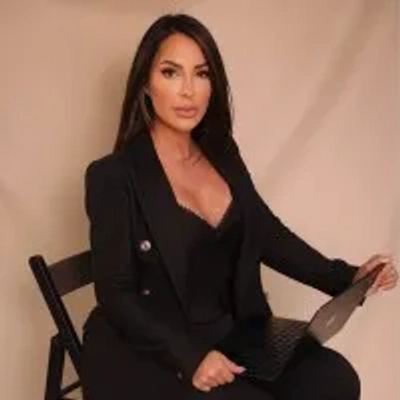
Blend Proactive Planning and Adaptive Strategies
Deviations during a batch run require a blend of proactive planning and adaptive strategies. From my medical background and business ventures, including the establishment of Profit Leap, I've learned the importance of diagnostics. Just as diagnosing a patient involves precise procedures, so does managing deviations—each anomaly needs swift identification and resolution.
In 2005, when I spearheaded a diagnostic imaging startup, we faced technical discrepancies early on. We applied a combination of real-time monitoring tools and flexible protocols. This approach resulted in a 20% reduction in error rates, ensuring precise imaging results.
I advocate for leveraging AI technology—like HUXLEY, which I co-designed—to anticipate and rectify deviations instantly. This minimizes potential risks while maintaining quality. Engaging teams in continuous improvement processes builds resilience against deviations, enhancing business efficacy across sectors from healthcare to technology.
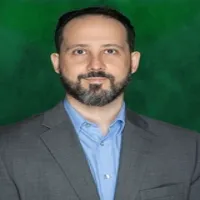
Halt Operations and Analyze Causes
During batch runs, deviations can be managed by first halting all operations to prevent further issues. Next, it is crucial to analyze the situation to identify what caused the deviation. Appropriate adjustments should then be made to the process to fix the problem.
Once the solution is implemented, the entire process must be carefully documented for future reference. After ensuring everything is in order, operations can be resumed with confidence. Always be prepared to act swiftly to maintain high-quality standards.
Monitor in Real-Time for Irregularities
Managing deviations effectively requires real-time monitoring of the batch run. This approach allows for the immediate identification of any irregularities as they occur. Promptly addressing these issues can prevent small problems from escalating into major disruptions.
The key is to maintain a vigilant eye on all processes and act quickly whenever deviations are detected. Continuous monitoring helps ensure a smooth and efficient production process. Embrace real-time monitoring to safeguard quality.
Implement Pre-Defined Contingency Plans
Having pre-defined contingency plans in place is an essential strategy for managing deviations during batch runs. These plans offer a clear set of actions to take when deviations occur, minimizing the time spent on decision-making. By following these pre-set guidelines, teams can swiftly handle unexpected issues without compromising on quality.
The routine training of all team members on these contingency plans ensures readiness and effective response. Implement these plans to keep your production line on track.
Integrate Automated Quality Checks
To maintain quality during batch runs, integrating automated quality checks at critical points in the process is highly effective. These automated checks serve as an early warning system, catching deviations as soon as they happen. This proactive approach enables timely corrections, reducing the risk of flawed products reaching the end of the line.
Automated systems can consistently check for various quality parameters, ensuring uniformity and standards are maintained. Invest in automation to enhance your quality control efforts.
Conduct Thorough Root Cause Analysis
Conducting thorough root cause analysis after a deviation occurs is vital for long-term process improvement. This method involves investigating the underlying cause of the deviation to prevent it from happening again. Once the root cause is identified, corrective actions can be taken to address the issue comprehensively.
This proactive measure not only solves the immediate problem but also strengthens the overall process. Make root cause analysis a regular practice to continually improve your operations.