4 Approaches to Continuous Improvement in Manufacturing Operations
Discover the transformative strategies for continuous improvement in manufacturing operations, as shared by seasoned industry experts. This article delves into the core principles and practical tools that drive efficiency and excellence. Learn from the insights of professionals who have successfully implemented Lean, Six Sigma, and other methodologies to elevate operational performance.
- Adopt Lean and Kaizen Principles
- Implement PDCA Cycle
- Focus on Streamlining for Efficiency
- Utilize Lean and Six Sigma Tools
Adopt Lean and Kaizen Principles
My approach to continuous improvement in manufacturing operations revolves around adopting the Lean Manufacturing methodology combined with the principles of Kaizen. These frameworks ensure efficiency, waste reduction, and sustained growth by promoting incremental, data-driven changes.
Lean Manufacturing allows us to identify and eliminate non-value-added processes, improving production flow and cost efficiency. For example, using Value Stream Mapping helps identify bottlenecks and streamline workflows. Similarly, techniques like 5S (Sort, Set in Order, Shine, Standardize, Sustain) create an organized, productive work environment.
Kaizen fosters a culture of continuous improvement by encouraging employees at all levels to contribute their insights. Weekly team meetings and Gemba Walks are integral to my strategy-they bring us closer to real operational challenges and spark actionable ideas for improvement.
I also leverage Six Sigma tools, such as DMAIC (Define, Measure, Analyze, Improve, Control), to address specific issues. One example is identifying quality defects through root cause analysis and implementing controls to prevent recurrence.
Regular audits, performance metrics tracking (like OEE-Overall Equipment Effectiveness), and embracing Industry 4.0 technologies, such as IoT-enabled monitoring, further enhance efficiency.
Ultimately, my approach prioritizes collaboration, employee engagement, and leveraging data to drive operational excellence and maintain a competitive edge in manufacturing.
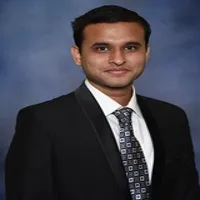
Implement PDCA Cycle
The PDCA (Plan, Do, Check, Act) cycle has been an excellent tool for our company; It's a structured approach that emphasizes incremental changes and collaborative problem-solving.
First, Plan by identifying an issue and developing a detailed solution with input from all stakeholders. Then, Do by implementing the plan on a small scale while closely monitoring the process. Next, check the results by analyzing data and feedback to determine the impact of the change. Finally, act by either integrating successful changes into standard operations or refining the approach based on the analysis. This iterative process allows individuals and teams to learn from each cycle, continuously optimize operations, and achieve ongoing improvement.
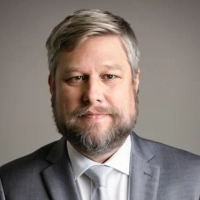
Focus on Streamlining for Efficiency
This is a great question. I find that many businesses focus on following a methodology rather than looking at the business in its entirety and solving bottlenecks that will not cause additional bottlenecks down the line. Methodologies are great if your business and business problems check the boxes, most do not. When strictly following a methodology you can often miss opportunities that are contributing to a problem but are not a part of the study per se such as the location of assembly, the intake or put away process or systems, or the layout of the current setup.
Our approach to continuous improvement in manufacturing operations focuses on streamlining for efficiency, reducing waste, minimizing shrinkage, and enhancing putaway time and accuracy. We analyze processes to identify bottlenecks and inefficiencies, implement solutions to optimize workflows and ensure resources are utilized effectively. By prioritizing accuracy in inventory management and reducing operational delays, we drive measurable improvements that lead to faster throughput, better resource allocation, and a more efficient operation overall.
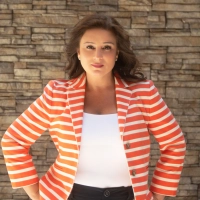
Utilize Lean and Six Sigma Tools
The Lean Manufacturing technique serves as the foundation for my strategy for ongoing manufacturing operations improvement. Lean offers an organized framework for continuous improvements by emphasizing waste reduction, process optimization, and customer value enhancement. We involve teams in finding inefficiencies and making little, gradual improvements by using tools like Kaizen events. This strategy is complemented by routine data gathering and analysis using methods like Six Sigma, which guarantee quantifiable and long-lasting benefits. This approach encourages creativity by giving staff members the freedom to share their ideas, which has improved productivity and lowered operating expenses.
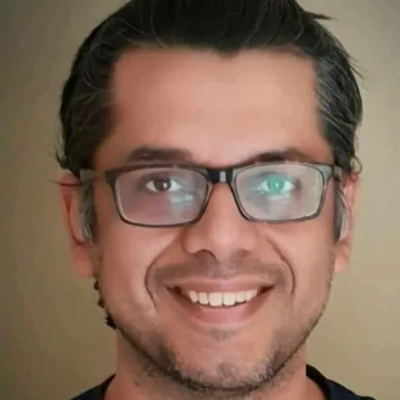