3 Applications and Advantages of 3d Printing in Production Processes
Delving into the transformative role of 3D printing in modern manufacturing, this article offers a deep dive into its applications and advantages. Insights from seasoned experts underscore the significance of this technology in customizing motorcycle parts, streamlining prototyping, and reducing production costs. These perspectives provide a comprehensive understanding of how 3D printing is revolutionizing production processes across industries.
- 3D Printing Essential for Custom Motorcycle Parts
- 3D Printing Enhances Prototyping and Production Efficiency
- 3D Printing Speeds Up Prototyping and Cuts Costs
3D Printing Essential for Custom Motorcycle Parts
At Schnurri-Racing, we're all about pushing limits, both on the track and in our workshop. As a motorcycle racing team, we don't build thousands of identical parts. We need exactly the right part, right now, and often that part doesn't even exist yet! That's where 3D printing (additive manufacturing) comes in. It's become absolutely essential for us, letting us create both finished parts and the tools we need to make other parts.
Take our ultralight engine cover for ZS/YX engines. Normally, making a custom, super-light engine cover with features like a built-in shift shaft support would mean tons of machining, multiple pieces, and a lot of waiting around. With 3D printing, it's a totally different story:
We can shave off over 200g compared to a standard cover. That might not sound like much, but on a race bike, every gram counts. The shift shaft support, which is critical for clean, fast gear changes, is printed right into the cover. No extra parts, no extra worries. If we need to tweak the design after testing, we can. We just print a new one in a few hours - no waiting weeks for a machine shop.
We can even print a rider's number and logo directly onto the cover. How cool is that? The two-part design and that built-in rain cover? Those are shapes that would be a nightmare (or impossible) to machine.
Our handlebar switches are another great example. These are the buttons that let our riders make adjustments on the fly. We build them using a mix of 3D printing and forged carbon fiber. We can create custom button layouts that are exactly right for each rider's hand and riding style.
Less weight on the handlebars means quicker handling. And we can quickly prototype different switch designs and see what works best.
The switch housings have to be extremely stiff so 3D printing is not always the best idea, but beyond that we are printing molds for creating carbon fiber parts which is where we can make forged carbon switch housings that tick all boxes.
3D Scanners, like the Creality CR-Scan Raptor, let us measure existing parts to quickly adapt them. Think of creating optimized fairings.
Basically, 3D printing gives us the freedom to create exactly what we need, exactly when we need it. It lets us be way more agile and creative than we could be with traditional methods. We're not just building parts; we're building a faster, more competitive race team.
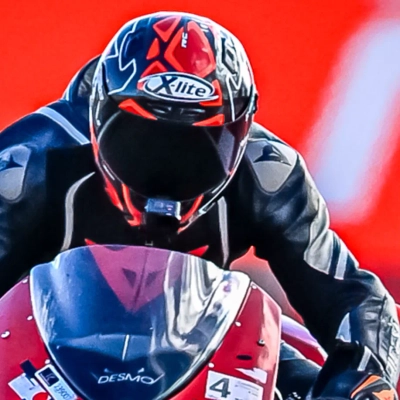
3D Printing Enhances Prototyping and Production Efficiency
In our company, we've integrated 3D printing (additive manufacturing) to improve both prototyping and production efficiency. For example, we use it to create custom jigs and fixtures for our assembly line, which has significantly reduced production downtime. With 3D printing, we can quickly iterate and test new designs without the delay of waiting for traditional tooling. One of the biggest advantages is the ability to produce highly precise and complex shapes that would be difficult or costly to achieve with conventional methods.
A great example of this was during a recent project, where we 3D printed a custom tool to hold a delicate component during assembly. The speed of printing and the ability to design a perfect fit allowed us to avoid delays and save costs that would have otherwise been spent outsourcing the part. This not only improved our production speed but also helped us maintain high-quality standards with minimal waste.
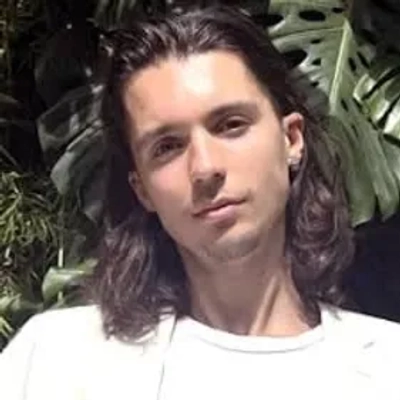
3D Printing Speeds Up Prototyping and Cuts Costs
The manufacturing clients we work with are using 3D printing to **speed up prototyping and cut production costs**. One client in the automotive space started 3D printing custom tooling and replacement parts on demand, cutting lead times from weeks to days. Instead of waiting for suppliers, they print exactly what they need in-house, reducing downtime and saving thousands. The advantage? **Faster iteration, lower costs, and way more flexibility**-3D printing isn't just for prototypes anymore, it's changing how production gets done.
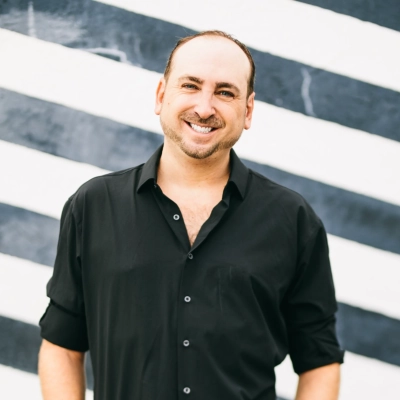